

The layout below has been manually adjusted to optimise for space. You can also define the stock size so components are laid out within the perimeter of the material. I recommend the tool which automatically copies bodies from the model and lays them out based on the smallest dimension (thickness). Now we can lay out the components for machining. We select the male component as the tool component and the female component as the target body.
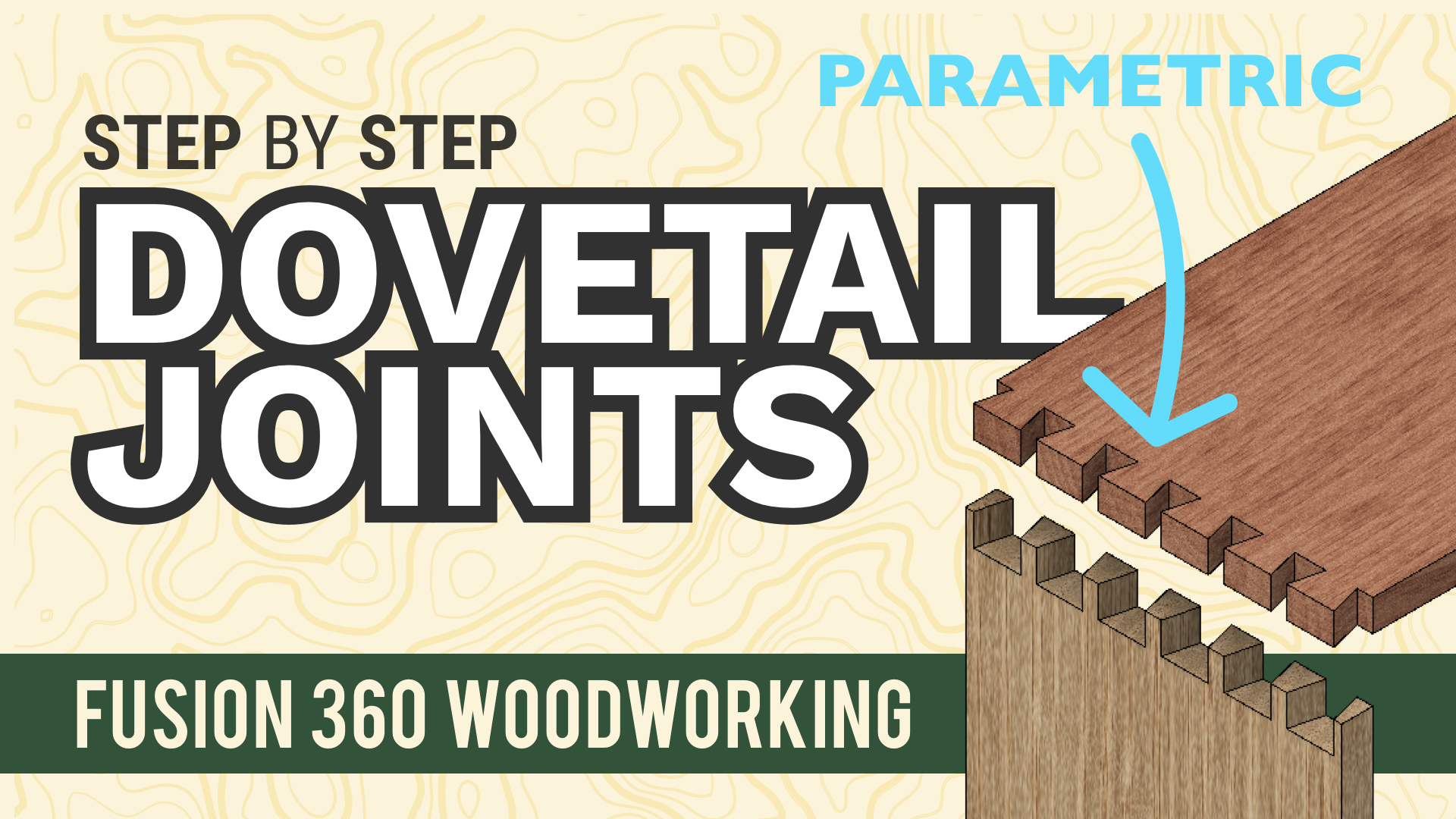
We can then use the combine tool to do a boolean operation. We will start by PRESSING the fingers into one of the components which is to become the male component. To do this We should use the user parameter MAT_THICKNESS to define the length that the fingers extend into the component. Next we can create some mirror planes through the axis of symmetry from which we can duplicate components to fill out the structure.įollowing this, we create the joints of our components. In this example there is a high degree of symmetry, so one side panel, one leg and one shelf only are modelled it this stage. Only create one component for each unique component at this stage (that way repetitious work can be avoided later). Next, create local sketches on the planes of principle components. This should contain the detail of where principle components are to be aligned. You should try to get most of the details that will drive the design in one sketch. Sketch (on paper) – the idea needs to be nearly fully formed before trying to model it, otherwise you will end up with a hot mess.
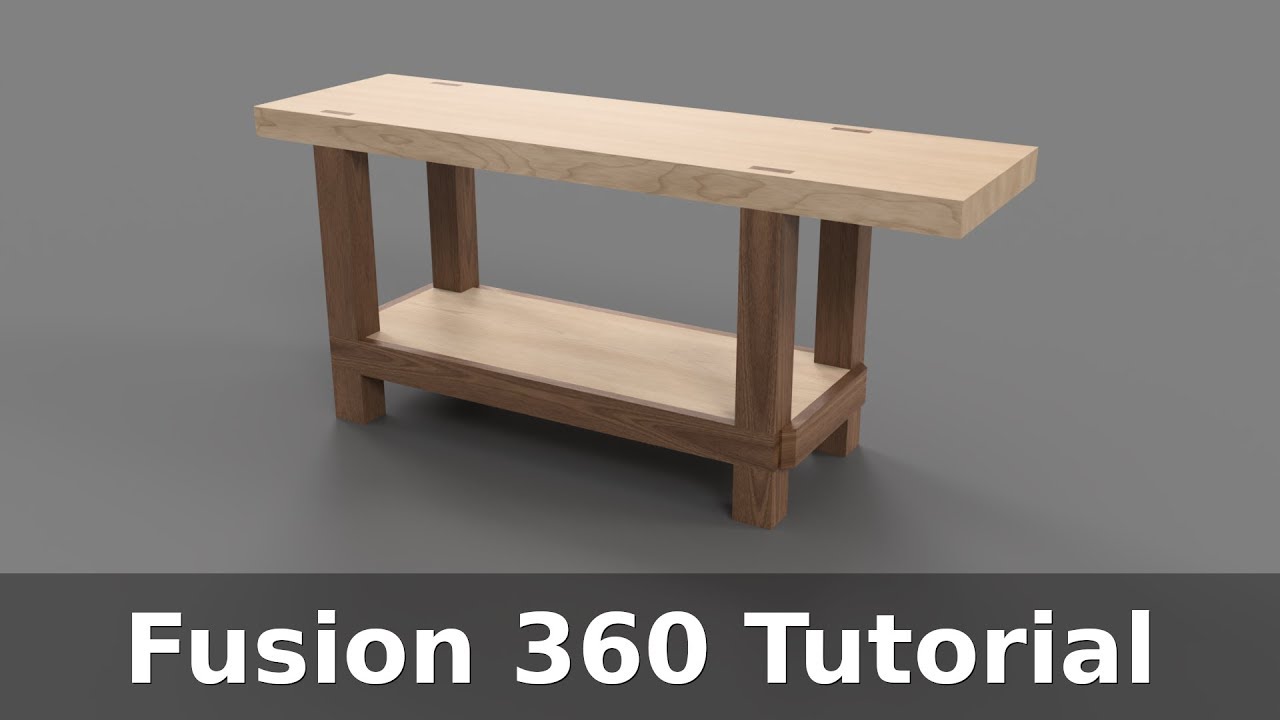
Doing this ultimately reduces design time and creates a model with a robust structure and timeline that allows modification in the future should it be required. The key strategy of the workflow is to work from a high level creating a framework and to work down adding detail as the design is developed. Key to success, is following a clear process that allows for modification as the design develops A winning workflow Although the example is specific to cabinetry, the principles can be applied for any kind of modelling. The following is a recommended process for design development in fusion 360.
